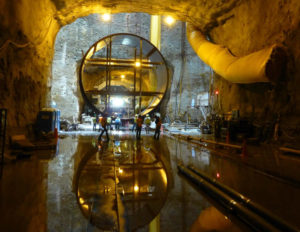
Chicago TARP-McCook 33 Foot Dia Steel Tunnel Liner-IL
ABSTRACT; Chicago Tunnel and Reservoir Plan system (TARP) including the McCook Main Line 33’ diameter tunnel liner, subassembly and installation process displayed by slide show photographs and commentary.
The Chicago Tunnel and Reservoir Plan (TARP) is a combined sewer overflow system devised in the 1970’s to control flooding in the metropolitan Chicago area. The system diverts storm water and sewage through 109 miles of large tunnels (9’-33’ diameter) into holding reservoirs for later treatment and averts sewer overflows causing harmful effects to Lake Michigan. When completed the TARP system will have a capacity of 17.5 billion gallons of storage and will complete one of the largest Civil Engineering mega projects in the United States.
The McCook Reservoir Main Tunnel is a central component to the TARP system as it connects the McCook Reservoir to Chicago’s Deep Tunnel system. The tunnel comprises a 33’ diameter liner which bifurcates into two rectangular cross section legs which control the flow of the system through high- head wheel gates. This tunnel pipe is one of the largest diameter steel tunnel liners in the country.
The main components to this project consist of excavating 1800’ of hard rock tunnel up to 40’ diameter which is located at the bottom of a 88’ diameter x 300’ deep shaft. Approximately 1300’ of the tunnel is concrete lined and 500’ of the tunnel includes a steel liner which bifurcates from a 19’x 32’ rectangular cross section to a 33’ diameter round section. The bifurcation legs accommodate flow control gates which are an integral feature of the assembly. The body of the liner utilizes “T” Steel rings wrapped around the liner shell on 16”-36” centers which allows the use of a relatively thin liner shell thickness of .75” considering the diameter of these components. This system was designed by Black and Veatch.
This slide show provides an overview of the project, plus details of the assembly and erection of the steel pipe sections. As these sizable sections could not be fabricated in shippable sized rings, the components to the 33’ diameter pipe sections and bifurcations were required to be fabricated in more manageable piece sizes. An initial task for the construction team was to maximize the pieces sizes which would minimize the onsite assembly requirements. In addition, the weight of some sub-assembled pieces was in excess of 180 tons and required rotational manipulation during installation. An added challenge was to perform this subassembly, fitting and welding of high strength steel in Chicago during winter conditions.