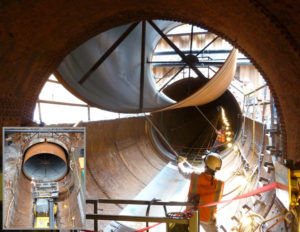
Pipe Rehabilitation Steel Tunnel Liner 147 inch Dia Blue Ridge Dam Penstock
Abstract; Steel Tunnel Liner 147” Diameter used to rehabilitation this penstock at TVA Blue Ridge Dam in Blue Ridge GA. The slide show provides a commentary and photographic review of the penstock liner manufacture and installation process for the following project:
The Toccoa Electric Power Company constructed the Blue Ridge dam and reservoir in 1925. At the time of construction, the project was the largest earthen dam in the southeast. The Tennessee Valley Authority (TVA) purchased the facility in 1939 for the production of power. The 25-mega watt powerhouse incorporated a 168” diameter riveted steel penstock from the intake structure to the powerhouse at the base of the dam. Shortly after construction, the penstock began to deform due to subsidence and external loading which prompted the need to reinforce the structure. A temporary remedy performed in the 1930’s included installing a girder within the penstock which is described as a vertical floor to ceiling wall approximately 18” thick dividing the penstock in halves for a distance of 160’ and weighing 300 tons. This girder/wall structure varied from solid steel at the base to concrete filled steel up to the ceiling. In an effort to insure public safety and meet dam safety standards TVA began a rehabilitation project in 2010.
The project consisted of three primary components. Dam and Intake structure stabilization and installation of a new penstock liner. The permanent remedy for the penstock remediation was to install a 147” steel liner within the existing 168” riveted steel penstock. National Welding Corp was hired by Garney Companies to perform most of the penstock specialty work and Northwest Pipe provided the penstock and materials. The initial task required removing the concrete filled steel girder which was accomplished using oxygen lances. The new steel liner which ranged in wall thickness from .875” to 1.00” could now be installed. This liner included butt welded pipe ends plus bell/spigot pipe ends and represented some of the largest expanded bell joints used in the United States. Reducers were used to connect the new liner to the existing penstock. Each new pipe segment weighed approximately 50,000 pounds and was required to be transported through an existing penstock with an irregular floor surface and 8” annular clearance. National devised a pipe transportation system which could carry the pipe approximately 1000’ through the penstock then position the pipe segments within the existing penstock. The new pipe segments were blocked in position, welded and the annular space was grouted. The reducer segments were particularly difficult as the full reducer rings required assembly within the penstock and without the benefit of overhead cranes. This mandated the careful coordination between Northwest Pipe and National to layout a buildable system. This was a very challenging project and was a unique remedy for a difficult condition.