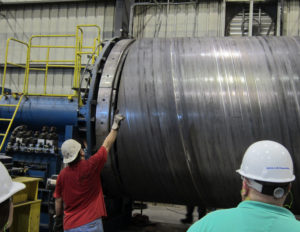
Steel Tunnel Liner 72 Inch Dia Staten Island to Brooklyn NY
Abstract; Steel Tunnel Liner 72 inch diameter which extends from under New York Harbor from Staten Island to Brooklynn. The slide show provides project history, commentary, photographs and solutions for the installation of a 72 inch diameter steel tunnel liner while correcting tunnel alignment deviations for the following;
The main components of this project included the mining and building of a segmented concrete tunnel underneath New York Harbor from Staten Island to Brooklyn and installing 9,460’ of 72”Ø X 0.625” bell and spigot single fillet welded steel tunnel liner. The adaptable installation methods, pipe bracing and necessity of adjustable bell and spigot joints in tunnel installations are the subjects of this paper. Early on in the planning/design process it was determined that the tunnel liner would be installed at a height of 17” to 21” from invert of tunnel to the flow line of the steel tunnel liner. As mining continued and experienced difficulties maintaining the planned tunnel elevations the design of the pipe carrier system as well as pipe bracing continually evolved and adapted to meet project needs. The final installation height varied from as low as 14” up to 44” from invert of tunnel to the flow line of the steel tunnel liner leaving as little as 7’ of clearance on the crown.
The planning and design of the steel tunnel liner installation was extended over a period exceeding 3 years and was constantly adapting to tunnel deviations caused by mining issues as well as delays including the flooding of the tunnel and TBM by hurricane Sandy in October 2012. Numerous delays mandated an accelerated schedule requiring installation and welding around the clock in order to meet the project deadline. The length of the tunnel itself presented numerous challenges to welding operations, access and most importantly welder/worker safety. With proper planning, the flexibility of bell and spigot lap joints, installation methods, bracing adjustability, high deposition welding processes and a team approach both the accelerated schedule and owner requirements were met. The paper will disclose the details of these operations and the lessons learned during the construction process.