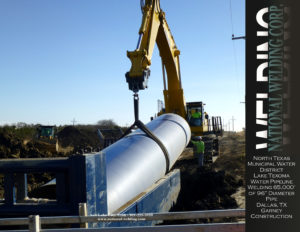
Weld-After-Backfill Application on steel pipelines
ABSTRACT; Weld-After-Backfill application is a method to install steel pipelines and is a growing practice. This short slide show provides photographs of the general steps for this process and provides caution against using incorrect materials for this method. This sequence of pipeline construction was first used in the late 1980’s on a pipeline in Texas. Since then, more than 50 major pipeline projects in the United States have been constructed using WAB.
A growing practice in steel water pipeline construction entails fitting bell & spigot pipe segments together, installing field joint coatings and backfilling the pipe prior to welding. Welding is then completed from the inside of the pipe after the pipe has been backfilled. Weld-after-backfill has proven to be successful in minimizing the length of open trench, improving project safety and speeding up pipeline laying, resulting in design, economic and safety advantages over traditional steel water pipeline construction methods. These advantages benefit the owner, designer, contractors and suppliers. WAB is recommended for projects with lap welded joints, which is the predominant joint design for most water pipeline installations.
The welding process, however, produces high temperatures on the pipe wall, which may damage some corrosion coatings. Research by Northwest Pipe, National Welding and Canusa-CPS was completed to evaluate various welding processes, measure temperatures and assesses the effects of the WAB sequence on exterior field joint coatings.